BATTERY
In the race to develop longer-lasting, safer, and higher-performance batteries, mechanical properties play a critical yet often overlooked role. As batteries undergo repeated charge and discharge cycles, their components experience significant mechanical stresses due to volume changes, interfacial instability, and particle rearrangement. These stresses can lead to cracking, delamination, and degradation of both electrodes and solid electrolytes, ultimately resulting in capacity fade, short circuits, or even catastrophic failure.
To design more reliable battery systems, it’s essential to understand how materials behave mechanically at every stage of cycling and across different length scales—from individual particles to bulk electrode layers. This includes properties such as elastic modulus, yield strength, fracture toughness, and time-dependent deformation (e.g., creep and relaxation).
The Alemnis Standard Assembly (ASA) is a fully automated, high-precision testing platform designed to measure the mechanical properties of microscale and nanoscale regions within complex material systems. Its unique in situ capabilities, especially when integrated into a scanning electron microscope (SEM), enable real-time observation and quantification of deformation, fracture, and time-dependent behavior under conditions that closely simulate real-world battery operation. This allows researchers to probe the real-time deformation and fracture behavior of battery materials under conditions that closely mimic actual operation. Whether testing single crystals, composite electrodes, or binder systems, the Alemnis Standard Assembly (ASA) platform delivers quantitative, localized mechanical data essential for optimizing battery materials and architectures.
For instance, the ASA precisely measured the longitudinal and transverse elastic moduli of individual carbon fibres at various lithiation stages. Compression tests were conducted on pristine IMS65 carbon fibres in air and ionic liquid environments. The results showed that the ionic liquid significantly affected the stiffness of the fibres.
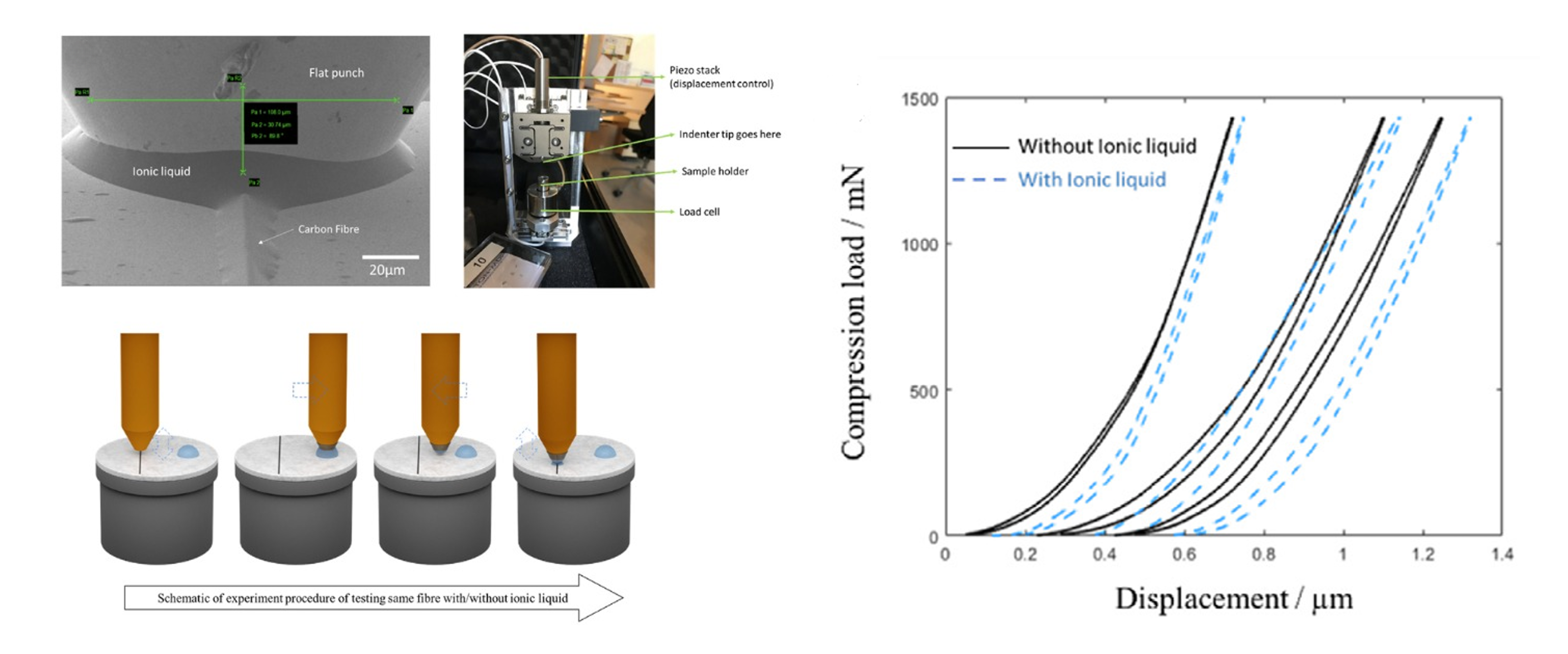
A schematic of the test procedure illustrates repeated compression on the same fibre with and without ionic liquid, while the compression curves compare pristine IMS65 carbon fibres in air and ionic liquid, revealing significant environmental effects on their mechanical response. (from Ref. 1)
Additionally, the time-dependent mechanical behavior of electrode binders was explored using the ASA to quantify viscoelastic relaxation properties of the composite electrode. With its high temporal resolution and customizable loading profiles, ASA provided data crucial for calibrating discrete element models (DEM). These simulations relied heavily on accurate indentation-based measurements of both the binder and active particle mechanics.

A SEM image displaying the polished indentation surface of the electrode (from Ref. 2)
The ASA’s ability to perform direct in situ compression and indentation testing also enabled the investigation of dislocation slip systems and critical resolved shear stresses in LiNi₀.₈Mn₀.₁Co₀.₁O₂ single crystals. The precise displacement-controlled and real-time SEM imaging enabled detection of slip activation and its role in crack formation. These insights were only possible through the ASA ability to apply controlled, localized stresses while visualizing microstructural changes live.
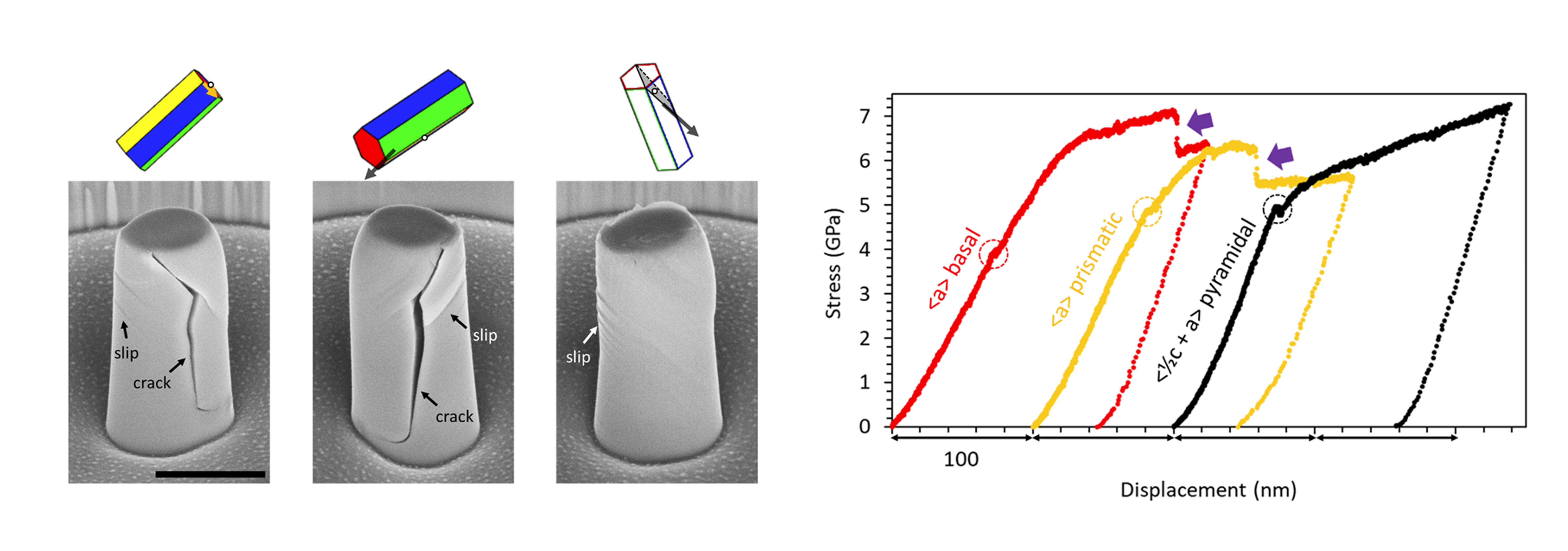
Post-deformation SEM images and mechanical responses of single crystal NMC811 micropillars demonstrated that the activation of slip systems and the occurrence of cracking depend on the crystal orientation relative to the loading axis (from Ref. 3).
Fracture of cathode secondary particles is a key degradation mechanism in lithium-ion batteries. Using a cono-spherical indenter within the SEM, the ASA enabled real-time fracture mapping of secondary LiNixMnyCozO₂ (NMC) particles. The fracture strength of LiNi₀.₈Mn₀.₁Co₀.₁O₂ (NMC811) secondary particles was measured via in situ microindentation, allowing dynamic visualization of crack propagation. Cracks initiated along grain boundaries between primary particles during compression using flat platens to mimic calendaring and a cono-spherical indenter to simulate particle-particle contact. Fracture typically occurred directly beneath the indenter tip and at the center of the secondary particles under platen compression.
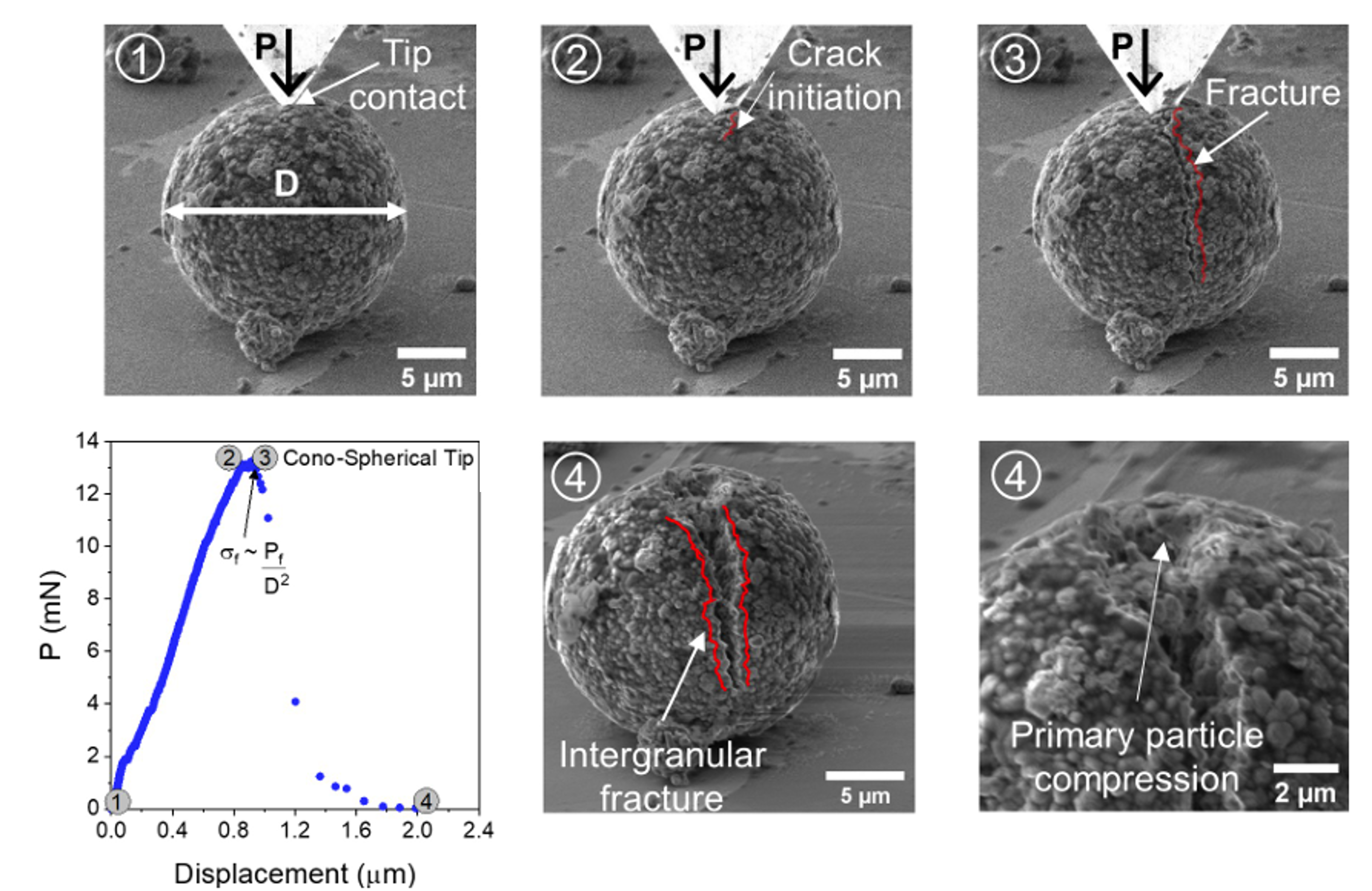
Sequential SEM images of a pristine NMC811 particle captured at different stages of indentation correspond to points along the load-displacement curve, with post-fracture imaging revealing the indentation crater and associated damage (from Ref. 4).
Finally, the ASA was used to assess the orientation-dependent compressive strength of single crystal NMC811 particles subjected to different charge rates. The ASA precise displacement control revealed anisotropic mechanical degradation patterns related to fast charging. This ability to correlate crystallographic orientation with strength evolution is critical for designing robust cathode architectures.
Together, these advanced capabilities of the Alemnis Standard Assembly highlight the crucial role of mechanical properties in battery performance and provide the insights needed to design next-generation, high-performance battery systems.
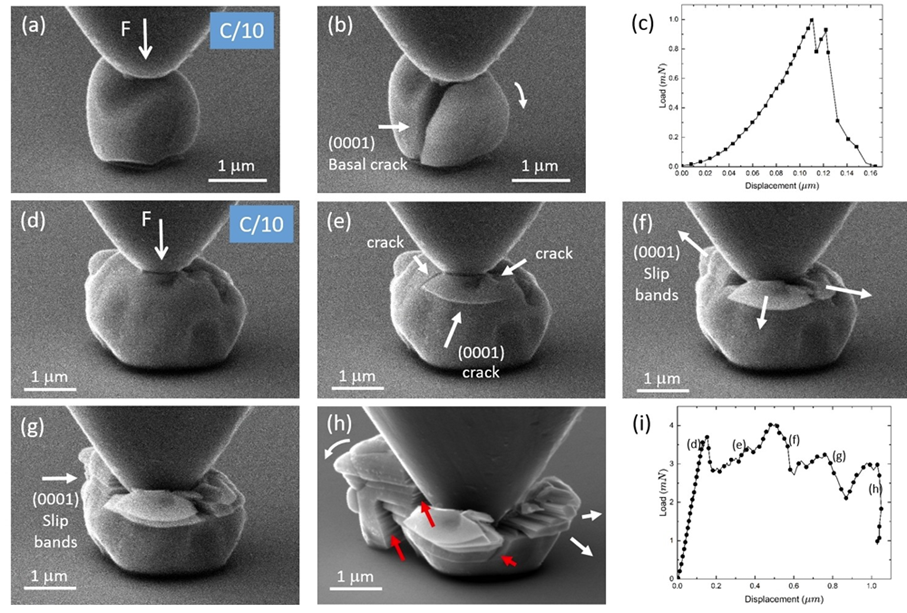
Compression tests of single-crystal NMC811 particles after 100 electrochemical cycles revealed orientation-dependent fracture behavior. Using the Alemnis stable, displacement-controlled indenter, deformation events could be clearly observed in situ and precisely correlated with specific points on the load-displacement curve (from Ref. 5).
Selected References
- S. Duan, A.H. Iyer, D. Carlstedt, F. Rittweger, A. Sharits, C. Maddox, K.R. Riemschneider, D. Mollenhauer, M. Colliander, F. Liu, L.E. Asp, Effect of lithiation on the elastic moduli of carbon fibres, Carbon, 185 (2021) 234–241. https://doi.org/10.1016/j.carbon.2021.09.037
- A. Lundkvist, P.L. Larsson, A.H. Iyer, E. Olsson, Discrete element modelling of the elastic-plastic and viscoelastic properties of a lithium-ion battery electrode layer, Powder Technology, 443 (2024) 119873. https://doi.org/10.1016/j.powtec.2024.119873
- S. Wang, Z. Shen, A. Omirkhan, O. Gavalda-Diaz, M.P. Ryan, F. Giuliani, Determining the fundamental failure modes in Ni-rich lithium ion battery cathodes, Journal of the European Ceramic Society, 43 (2023) 7553–7560. https://doi.org/10.1016/j.jeurceramsoc.2023.08.021
- L. Wheatcroft, A. Bird, J.C. Stallard, R.L. Mitchell, S.G. Booth, A.J. Nedoma, M.F. De Volder, S.A. Cussen, N.A. Fleck, B.J. Inkson, Fracture testing of lithium‐ion battery cathode secondary particles in‐situ inside the scanning electron microscope, Batteries & Supercaps, 6 (2023) e202300032. https://doi.org/10.1002/batt.202300032
- A. Jangde, M. Kumar, İ. Tuğrul Gülenç, L. Wheatcroft, B.J. Inkson, Mechanical properties of cycled single crystal LiNi₀.₈Mn₀.₁Co₀.₁O₂ (NMC811) particles, Batteries & Supercaps (2025) e202400691. https://doi.org/10.1002/batt.202400691