DIGITAL IMAGE CORRELATION
In recent years, the mechanical behavior of materials at microstructural scales has been increasingly studied with numerical or experimental approaches. The development of Digital Image Correlation (DIC) has allowed kinematic measurements to be made via SEM imaging to provide spatially dense 2D or even 3D fields.
Kinematic measurements with DIC require gray level texture images whose dynamic range should be as large as possible with high local contrast. If the natural texture of the material does not provide such contrast, different marking techniques can produce the suited artificial texture on the surface of interest. In the context of SEM imaging, the deposition of small “speckles” can be achieved by nanoparticle deposition techniques or by UV photolithography.
Electron beam induced deposition (EBID) is a synthesis technique which uses the SEM electron beam and stimulates a localized reaction of precursor species resulting in a nanoscale synthesis technique which can conveniently grow nanospeckles via a prescribed electron beam raster sequence. If such nanospeckles are deposited onto a micropillar which is compressed using the Alemnis Standard Assembly (ASA) then a series of high resolution SEM images will allow the strain to be mapped using DIC.
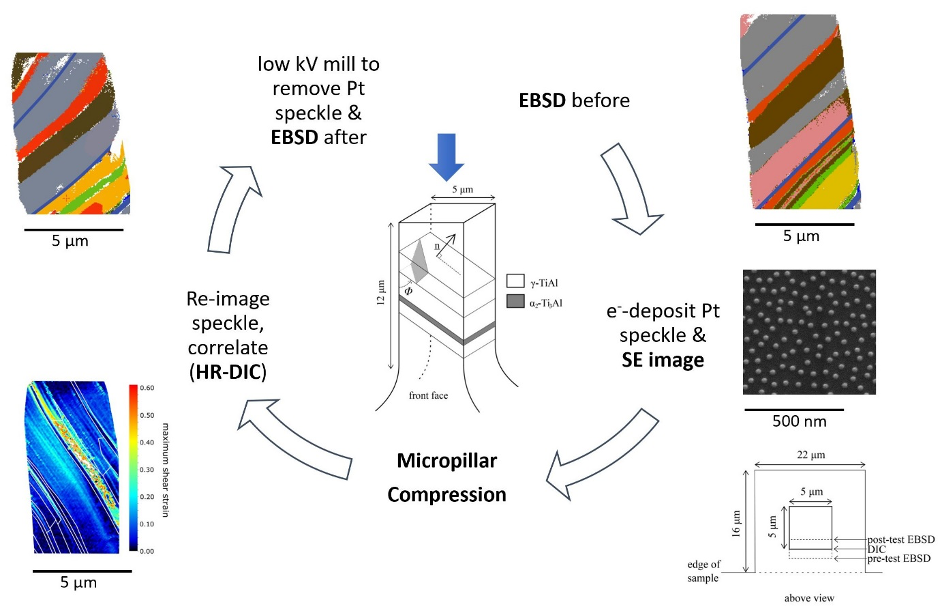
Typical procedure used for strain mapping of a micropillar with DIC: EBSD scan, deposition of nanospeckles, micropillar compression test, strain mapping and final EBSD (Courtesy of Thomas Edwards, EMPA, Thun, Switzerland)
A typical procedure is to fabricate the micropillar using Focused Ion Beam (FIB) milling and then perform an additional milling step to improve the surface finish for Electron Backscatter Diffraction (EBSD). The surface is then speckled using a suitable source material (e.g., gold, platinum, etc..) and the micropillar undergoes the mechanical compression test, after which the strain map is generated by correlation of the pre- and post-deformation images using a suitable software. Many Alemnis users are currently using DaVis produced by LaVision, Germany (https://www.lavision.de/en/products/davis-software/). In some cases, a further milling step may be used to remove the speckle pattern from the tested micropillar and thus allow a second series of EBSD scans to be made.
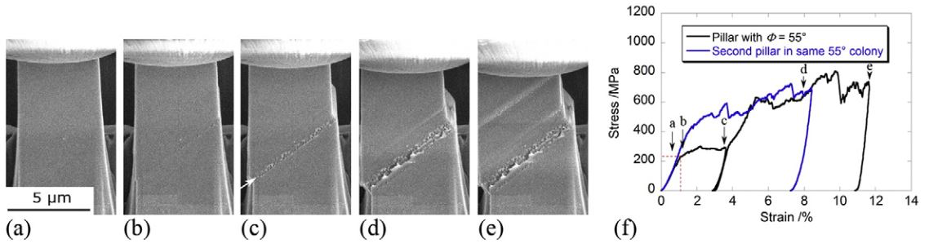
Example of longitudinal twinning of Titanium Aluminide (Ti-45Al-2Mn-2Nb(at.%) + 0.8vol.%TiB2) at 25°C with secondary SEM video frames (a)-(e) and the stress-strain curves in (f). The white arrow in (c) corresponds to the location of the slip bands (from Ref. 2)
Some good examples are shown for a Titanium Aluminide micropillar subjected to microcompression testing. The micropillars were made sufficiently small so that they would not contain any grain boundaries: hence longitudinal twins could be unconstrained and DIC could be used for identifying where dislocation glide occurred, particularly adjacent to twinned lamellae.
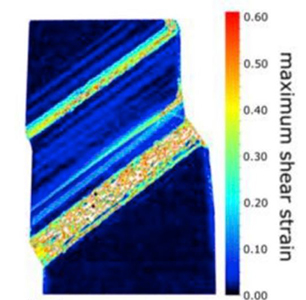
Example of longitudinal twinning of Titanium Aluminide (Ti-45Al-2Mn-2Nb(at.%) + 0.8vol.%TiB2) at 25°C together with the corresponding DIC strain map (from Ref. 2)
The ASA mounted with a High Temperature Module (HTM-800) ADD LINK can be effectively used to study the high temperature effects of longitudinal twinning in Titanium Aluminide. The critical resolved shear stress for longitudinal twinning was found to increase monotonically with temperature up to 700°C. This was in agreement with an increased twin shear fault energy with temperature, based on literature models for twin formation. Ref. 3 gives a good overview of the experimental procedure for achieving reliable data at very high temperatures with the ASA and HTM-800.
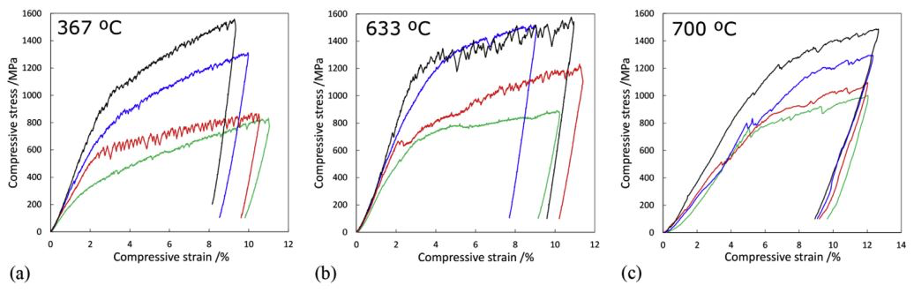
High temperature stress-strain curves for TiAl micropillar compression tests at 367°C, 633°C and 700°C, indicating both the extremes of load attained and the varied degree of serration in the plastic region (from Ref. 3)
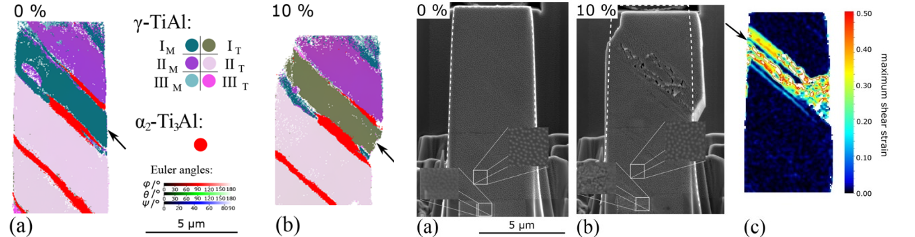
Example of a TiAl micropillar before and after compression at 700°C with major slip planes arrowed in both the EBSD images (left) and the DIC strain map (far right). The speckle pattern is visible in the zoomed portions of the secondary SEM images (from Ref. 3)
Selected References
- F. Di Gioacchino & W. J. Clegg, Mapping deformation in small-scale testing, Acta Materialia 78 (2014) 103-113. https://doi.org/10.1016/j.actamat.2014.06.033.
- T. E. J. Edwards, F. Di Gioacchino, R. Munoz-Moreno, W. J. Clegg, Deformation of lamellar TiAl alloys by longitudinal twinning, Scripta Materialia 118 (2016) 46-50. https://doi.org/10.1016/j.scriptamat.2016.03.004.
- T. E. J. Edwards, F. Di Gioacchino, G. Mohanty, J. Wehrs, J. Michler, W. J. Clegg, Longitudinal twinning in a TiAl alloy at high temperature by in situ microcompression, Acta Materialia 148 (2018) 202-215. https://doi.org/10.1016/j.actamat.2018.01.007.
- R. D. Jones, F. Di Gioacchino, H. Lim, T. E. J. Edwards, C. Schwalbe, C. C. Battaile, W. J. Clegg, Reduced partitioning of plastic strain for strong and yet ductile precipitate-strengthened alloys, Scientific Reports 8(1) (2018) 8698. https://doi.org/10.1038/s41598-018-26917-0.
- T. E. J. Edwards, F. Di Gioacchino, A. J. Goodfellow, W. J. Clegg , Slip bands in lamellar TiAl during high cycle fatigue microcompression by correlative total strain mapping, diffraction orientation mapping and transmission electron imaging, International Journal of Fatigue 124 (2019) 520-527. https://doi.org/10.1016/j.ijfatigue.2019.03.016.
- T. E. J. Edwards, F. Di Gioacchino, A. J. Goodfellow, G. Mohanty, J. Wehrs, J. Michler, W. J. Clegg, Deformation of lamellar γ-TiAl below the general yield stress, Acta Materialia 163 (2019) 122-139. https://doi.org/10.1016/j.actamat.2018.09.061.
- L. Chen, T. E. J. Edwards, F. Di Gioacchino. W. J. Clegg, F. P. E. Dunne, M-S Pham, Crystal plasticity analysis of deformation anisotropy of lamellar TiAl alloy: 3D microstructure-based modelling and in-situ micro-compression, Int. Journal of Plasticity, 119 (2019) 344-360. https://doi.org/10.1016/j.ijplas.2019.04.012.
- T. E. J. Edwards, F. Di Gioacchino, A. J. Goodfellow, G. Mohanty, J. Wehrs, J. Michler, W. J. Clegg, Transverse deformation in a lamellar TiAl alloy at high temperature by in situ microcompression, Acta Materialia 166 (2019) 85-99. https://doi.org/10.1016/j.actamat.2018.11.050.