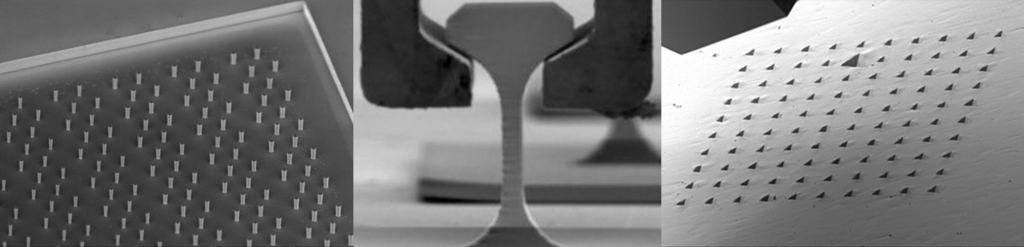
Understanding the Effects of Loading Rate in Nanoindentation Testing
Loading rates refer to the speed at which a nanoindenter applies force to a surface. It is instrumental in influencing the material’s mechanical response. Thus, loading rates help reveal time-dependent behaviour under stress. This helps researchers explain properties like elastic modulus, fracture toughness, hardness, etc. This blog post delves deeper into the recent research that illuminates the effects of loading rate in nanoindentation, focusing on diverse materials such as SU-8 polymer, microscale glass, and nanocrystalline nickel.
High Strain Rate Nanoindentation of SU-8 Polymer
In a groundbreaking study, Cherukuri et al. explored the mechanical properties of SU-8, a negative photoresist polymer essential in the fabrication of micro- to meso-scale structures, at high strain rates (up to 10^3 s^-1) using in situ micropillar compression and nanoindentation within a SEM environment. Their work highlighted the consistent mechanical properties of SU-8 across a wide range of strain rates, with no observable change in deformation mechanisms even at high strain rates. This is particularly noteworthy considering the SU-8 polymer’s extensive application in MEMS, where it’s exposed to various impact conditions. The researchers also introduced an innovative experimental protocol to minimize resonance amplitude during unloading, enabling the accurate extraction of modulus and hardness values using the Oliver-Pharr method.
Dynamic Plasticity and Failure of Microscale Glass
Ramachandramoorthy et al. conducted in situ high-strain-rate experiments on fused silica micropillars at strain rates up to 1335/s, observing a ductile-brittle-ductile transition in failure modes as strain rates increased. This study is crucial for understanding the dynamic mechanical properties of microscale glass, especially given its emerging role as a robust alternative to silicon in MEMS applications. The research revealed that at intermediate strain rates, the deformation in glass transitions through a serrated flow regime, characterized by the sequential propagation of individual shear bands. A transition to a more homogeneous deformation regime was observed at higher strain rates, attributed to the simultaneous nucleation of multiple shear bands and dissipative deformation heating.
Nanoindentation of Nanocrystalline Nickel
Schwiedrzik et al.’s nanocrystalline nickel (ncNi) study focused on its dynamic cryo-mechanical properties. They synthesized ncNi micropillars and complex micro-lattices using template-assisted electrodeposition and two-photon lithography, testing them at cryogenic temperatures and strain rates ranging from 0.001 to 500 s^-1. This research is pivotal in establishing microstructure-mechanical property relationships under extreme conditions, a necessity for the application-relevant design of metamaterials. Their findings showed minimal strain hardening and a low strain rate sensitivity in ncNi, which slightly increased at sub-ambient temperatures. This low strain rate sensitivity is critical for precision watchmaking applications and sensitive microsensors’ impact protection.
Learn more about nanoindentation testing with Alemnis
In sum, these studies collectively underscore the importance of understanding material behavior under varying strain rates, particularly in applications requiring high reliability and efficiency at the microscale. The advancement in high-strain rate nanoindentation testing techniques bridges the gap between theoretical knowledge and practical application. It contributes significantly to developing materials with tailored properties for specific industrial applications. This research is instrumental in paving the way for designing and optimising materials and devices that can withstand dynamic loading conditions, thus enhancing their performance and longevity in real-world applications.
The effects of loading rate in nanoindentation testing are multifaceted and significantly impact the mechanical characterization of materials. Dynamic mechanical analysis can help you understand the impact of stress and strain on a material. However, it is also crucial to have a basic understanding of the effects of loading rate. That way, you can produce an accurate material assessment.
This knowledge not only aids in predicting material behavior under different conditions but also in designing materials with tailored properties for specific applications.
At Alemnis, we recognize the critical role that nanoindentation testing plays in this journey. Our dedicated focus on expanding the frontiers of nanoindentation, particularly in challenging environments like high temperatures, addresses a wide range of material characterization needs.
Whether you are exploring the mechanical characterization of thin films, assessing the elastic recovery of novel materials, or delving into the time-dependent behavior of complex composites, Alemnis is your innovation partner. Our state-of-the-art equipment, optimized for various sample surfaces and sample preparation techniques, ensures precision and reliability. With our advanced indentation tip technology and the ability to control indentation depth accurately, we can reveal the intricate details of material behavior under varying applied forces.
We offer solutions that range from high-load applications to delicate, precision-focused tests. The displacement curves generated using our tools provide valuable insights into the rates that depend on material responses, facilitating comprehensive mechanical characterization.
At Alemnis, we are committed to pushing the boundaries of what’s possible in nanoindentation. To learn more about how our solutions can revolutionize your material testing capabilities, especially at high temperatures, visit us at Alemnis high-temperature nanoindentation. Discover a new dimension in material science where precision meets innovation.
References & Further Reading
1. Cherukuri, R. et al. Materials Letters 358 (2024) 135824.
2. Ramachandramoorthy, R. et al. Nano Lett. 2019, 19, 2350−2359.
3. Schwiedrzik, J. et al. Materials & Design 220 (2022) 110836.